
Boken Consulting
Lean & Six Sigma
Nossa Metodologia
Lean Manufacturing
Nossa filosofia fundamental de trabalho é o Lean Manufacturing, que consiste num sistema produtivo, desenvolvido pela Toyota, no Japão, durante o período pós-guerra. Este sistema é composto de um conjunto de técnicas e ferramentas, que buscam criar um fluxo contínuo através da cadeia produtiva, embutir a qualidade nos processos e eliminar os desperdícios, reduzindo custos e, ao mesmo tempo, melhorando a qualidade e aumentando a flexibilidade.
​
É muito comum representar esta metodologia na forma de uma casa, onde:
-
A base contém o trabalho padronizado e a melhoria contínua, promovendo a estabilidade;
-
Os dois pilares representam os princípios: fluxo e qualidade;
-
O telhado representa os objetivos, que são a Satisfação do Cliente e o Desenvolvimento Humano;

Ao contrário de outras técnicas para aumentar a produtividade, a grande vantagem do Lean Manufacturing é que essa metodologia não exige grandes investimentos. O grande diferencial é que, ao invés de focar na melhoria dos processos que agregam valor, ou seja, processos que transformam o produto, o Lean foca em combater os desperdícios, ou seja, processos que não agregam valor ao produto ou serviço.
​
A metodologia Lean classifica os desperdícios em 8 tipos:
​
​
​
​
​
​
​
​
​
​
​
​
​
​
Muitas vezes, os desperdícios consomem muito mais recursos e custam muito mais do que os próprios processos de agregação de valor. Outra grande vantagem é que, combater os desperdícios é muito mais fácil, mais rápido e requer menos investimentos, do que otimizar processos de transformação.
Para obter ganhos em processos de agregação de valor, muitas vezes aplicamos a automação, que exige massivos investimentos em máquinas, computadores, sistemas de controle, etc. Comparado à automação, o Lean pode ser implementado com um mínimo investimento em treinamentos e melhor aproveitamento do capital humano.
​
Tomemos como exemplo um processo de empacotamento. Você poderia investir em uma grande máquina de embalagem automática, visando reduzir o custo de mão de obra com este processo, ou poderia eliminar os desperdícios, melhorando o layout para reduzir o deslocamento dos operadores para buscar material no estoque (transporte), implantar um sistema kanban para eliminar o tempo que os colaboradores ficam aguardando a chegada de produtos para embalar (espera), criar instruções de trabalho padronizadas para evitar erros de embalagem (retrabalho), etc.
Para aplicar o Lean é preciso aprender a enxergar os desperdícios e a partir daí você vai começar a encontrar oportunidades de melhoria em tudo, em qualquer processo empresarial ou até mesmo na sua casa e na sua vida pessoal.
​
Logicamente, este é um exemplo simplista e didático para explicar o que é e como funciona a metodologia, porém o Lean não se limita a combater os desperdícios. Existe uma diversidade de outras ferramentas e uma das mais populares é, sem dúvida, o 5S. Porém, também existem outras ferramentas, que são utilizadas para nivelar a produção (Heijunka), para embutir a qualidade (Poka-Yoke), para criar fluxo puxado (Kanban), para mapear os processos (VSM), etc.
​
Enfim, resumidamente a grande virtude do Lean é permitir alcançar ótimos resultados, reduzindo custos e melhorando a qualidade, através da aplicação de técnicas simples e com pouquíssimo investimento.

Six-Sigma
O segundo eixo, igualmente importante na formação da Boken é o Six-Sigma, que consiste num conjunto de ferramentas para melhoria de processos, desenvolvida originalmente pela Motorola em 1985 e que hoje é amplamente utilizada na indústria.
​
Em sua essência, o Six Sigma busca reduzir a variação nos processos, aumentando a previsibilidade e minimizando as falhas ou defeitos.
​
A variação está presente em vários processos e oportunidades podem ser encontradas em todos segmentos da indústria e de serviços. Na logística, por exemplo, imagine uma empresa que promete um prazo de entrega de 10 dias. Vários fatores podem influenciar este prazo, por exemplo, a disponibilidade do produto, a consolidação de pedidos, as condições das estradas, etc. Por isso, em alguns casos, a entrega pode ocorrer em 7 dias, em outros casos, em 13 dias. É fácil imaginar como essas incertezas podem causar insatisfação do cliente, não é?
​
Na indústria de bebidas, um outro exemplo, imagine um produto vendido numa latinha de 350 ml. O processo de enchimento é feito numa linha automática e o quantidade de líquido depende de uma série de variáveis como, por exemplo, a pressão da bomba, a viscosidade do líquido, o tempo de enchimento, temperatura do ambiente, etc. Mesmo que o equipamento esteja muito bem calibrado, pequenas variações ocorrerão e, por isso, alguns consumidores poderão comprar latinhas com 353 ou 347 ml. Para evitar reclamações, o que muitas empresas fazem é ajustar a máquina para um valor um pouco acima do valor da especificação, por exemplo, programar a máquina em 355 ml.
​
A questão principal é que essas variações representam sempre um desvio de qualidade, que pode gerar perdas financeiras para a empresa ou até arruinar completamente a imagem de uma marca. Na era das redes sociais, imagine o estrago que pode ser causado pela reclamação de um cliente, que comprove ter sido lesado numa compra, porque a quantidade de produto contida na embalagem era menor do que a anunciada no rótulo.
​
Por outro lado, muitas vezes essas variações geram perdas difíceis de detectar. Ainda sobre o exemplo da latinha de bebidas, os 5 ml entregues a mais, em média, em cada latinha de bebida, representam uma perda de "apenas" 1,43%, um valor que pode facilmente ficar escondido entre outras perdas que ocorrem no processo. No entanto, multiplicando pelo volume de produção, que é de alguns milhões de latas vendidas por ano, certamente chegaremos a um impacto financeiro bastante expressivo.
Para combater a variação nos processos, a metodologia 6-Sigma conta com um aparato de ferramentas estatísticas, que aplicadas em uma sequência lógica, permitem aumentar a confiabilidade nos processos. Esta sequência lógica é conhecida como método DMAIC, que é muito parecido com o popular PDCA, porém com uma etapa de planejamento mais profundamente detalhada.

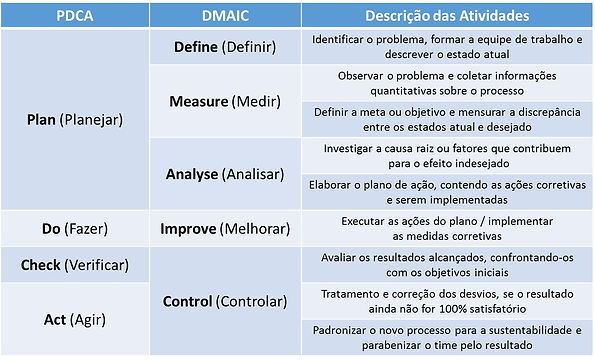
A origem e o significado do termo "Six Sigma", resulta de um parecer estatístico, no qual estão relacionados o desvio padrão e os limites de especificação de uma determinada variável.
Para quem ainda não é muito familiarizado com esses termos estatísticos, podemos dizer resumidamente que o desvio padrão representa a variação, dispersão ou incerteza de uma determinada medida, em torno do seu valor médio, para uma determinada amostra da população.
Uma das etapas de um projeto 6-Sigma é promover estudos de capacidade, que consistem em fazer observações e coletar amostras para medir estatisticamente o número de desvios padrão, compreendidos entre a média do processo e o limite de especificação mais próximo. Essa medida é comumente representada em unidades de sigma, representada pela letra grega σ (sigma) que representa o desvio padrão.
​
Basicamente, a teoria estatística diz que se couberem 6 desvios padrão entre a média do processo e o limite de especificação mais próximo, então praticamente não haverá itens fora das especificações.
​
​
Quando o desvio padrão do processo aumenta ou quando a média do processo move-se para longe do centro da tolerância, menos desvios padrão caberão entre a média e o limite de especificação, diminuindo o número de sigmas dentro dos limites de controle e aumentando a probabilidade de itens fora de especificação.
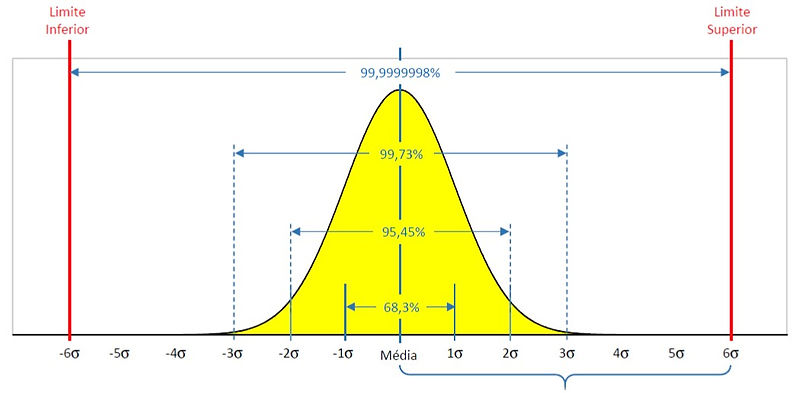
Lean & Six Sigma
​Combinadas, essas duas metodologias formam o eixo Lean & Six Sigma, uma metodologia extremamente poderosa, que permite alcançar resultados quantitativos extraordinários, em curto prazo e com baixo investimento.
